Since 2013 Koenig & Bauer MetalPrint awards outstanding performance with the “High-Performance Metal Decorator of the Year”. It was established to honour customers who use products of Koenig & Bauer to demonstrate achievement beyond the scope of everyday performance in the field of metal decorating.
This time Glud & Marstrand A/S received the award. The Danish canmaker has set a new benchmark in the metal decorating world by optimising their production process with a unique line configuration. With the highly-automated 6-colour MetalStar 3 press installed in front of a tandem coating line they have built a line configuration which is really one of a kind. With a length of 140 m it is not only the longest decorating line that has ever been built but also extremely economical and cost-effective. Operating such a long and complex line, in which three individual processes are combined in one line, is a hugely challenging task and requires a very well-organised print shop, a highly experienced and educated staff, and of course a great passion.
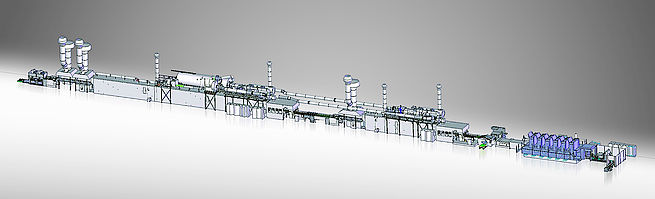
The award was accepted by Glud & Marstrand’s senior printing manager Henrik Olsen, chief executive Brian Nielsen and Isaias Zapata, managing director of Food & GL at Envases Universales, the Mexico-based packaging manufacturer that owns Glud & Marstrand.
Glud & Marstrand is one of the most experienced user of so-called tandem coating lines in which the coating and drying takes place twice in one process step. In 2016 Glud & Marstrand decided to invest in a new MetalStar3 installed in front of a tandem coating line making it the world’s longest metal decorating line. The line was equipped with an automatic pile changer, specially developed for metal printing. It changes a pile within 20-30 seconds and automatically removes the empty pallet. Up to three pallets up to 2,5 t can be lined up on the roller conveyor to be processed one after the other. The new MetalStar 3 has been equipped with CleanTronic Synchro, DriveTronic SRW and ErgoTronic ACR to reduce makeready times. In addition it is designed for the use of UV inks and equipped with interdeck UV dryers and an end-of-press UV dryer. The coated sheets are dried in a 150 m-long pre-dryer and a 36 m-long main drying oven. An EcoTNV (thermal incinerator) was integrated into the line to drastically reduce the high energy consumption.
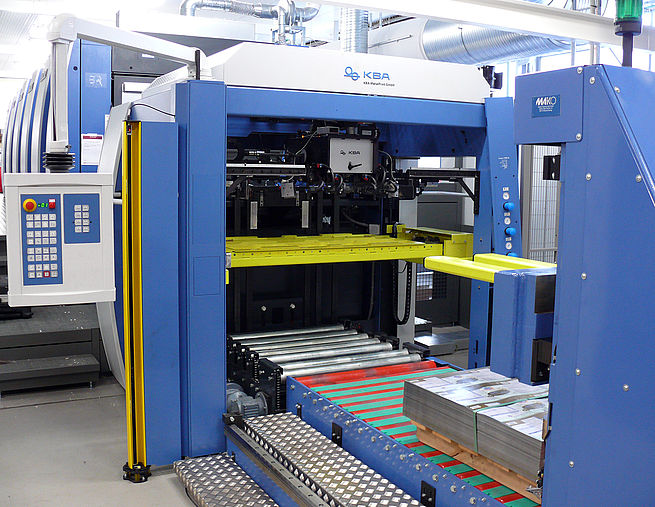