New wide belt conveyor system for UV dryer with food approved belts
Koenig & Bauer MetalPrint launched a new wide belt conveyor for UV drying systems. The conveyor system is equipped with a new belt technology. The belts are FDA compliant and do not contain silicones or PTFE. The pollution of the machine and the contamination of the printed sheets with dust particles is prevented, as the belts are abrasion-free.
Each belt is pneumatically tensioned by a new designed rocker arm which allows an adjustment of the tension of each belt individually to guarantee a stable transport of the sheet. The assembly of the belts is done via a plastic thread. Means the belts do not have to be glued which reduces the change time significant and also provides always a good quality of the splice.
By design, the conveyor is equipped with fans which are used to cool the belts in order to extend the lifetime of them and also to gently generate a vacuum effect for a safe transport of the sheets and with no risk of slipping.
The belt conveyor is equipped with 4 wide belts with each 250 mm width. Due to the arrangement of the belts, no format adjustments are necessary as the minimum and maximum format of the MetalStar 3 and Mailänder 280 is covered by the outer belts.
The new conveying system can be equipped with UV drying systems from Koenig & Bauer MetalPrint and also with drying systems from other suppliers.
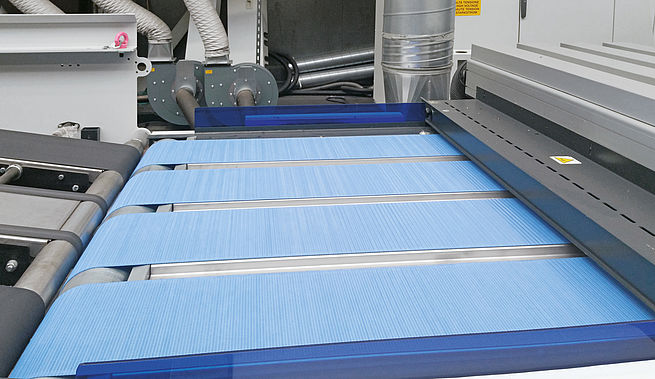
Drying automation with ModEX
With the modular data exchange system ModEX by Koenig & Bauer MetalPrint, conventional drying ovens are taking a step towards modern technology. It is the answer for actual market demands for automation, process stability and operator relief.
ModEX is equipped with a recipe management system, which can contain up to 100 recipes for the oven settings for various parameters, e.g. temperature and fan frequencies for each heating zone or wicket pre-heating settings. The settings for each recipe are made either by oven specialist from Koenig & Bauer MetalPrint or by oven specialists at the customer.
Job information are transferred to the coating line via the customer system, such as an Management Information System (MIS) or Production Planning System (PPS). As the job data such as material, used coating and correspondent recipe are known to the oven, the operator does not have to adjust the oven according to the next job. The oven adjusts itself to the correct setting for the next job being coated. This means 2 big advantages:
1. The setting of the oven is no longer depending on manual input by the operator, which increases the safety and reduces spoilage
2. The make – ready time is shortened, as the operator does not have to take care of the oven manually
The loading of the settings for the next job is performed by ModEX automatically and sequential. Means, that heating zone 1 is automatically setting up for the next upcoming job as soon as the last sheet of the previous job leaves heating zone 1.
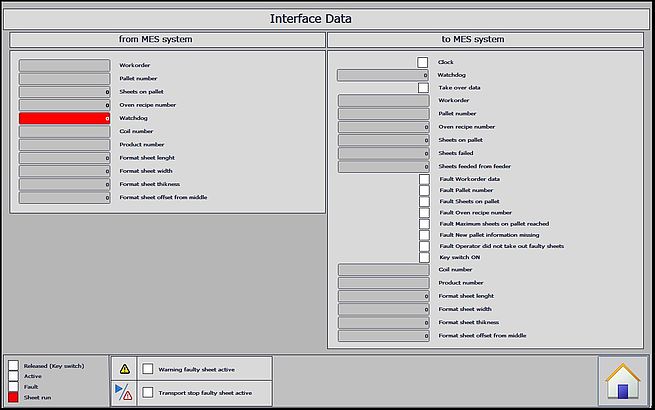