- Maximum flexibility paired with ultimate production quality
- Enhanced flexibility cushions production peaks at PS PrintService
- Digital networking enables an end-to-end workflow
PS PrintService has worked with metal decorating presses from Koenig & Bauer MetalPrint ever since it opened its plant in Neuhaus-Schierschnitz in the German state of Thuringia in 2004. Operating as a local, mid-size company, its main business is the decoration and finishing of metal sheets for use in the production of crown corks and aluminium screw caps. In addition, different designs are printed for food packaging of all kinds, as well as fancy cans and tins for cosmetics products.
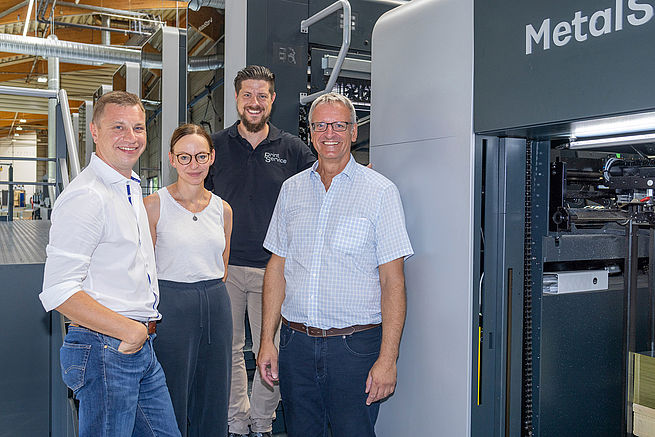
With its investment in a new, six-colour printing line, PS PrintService is expanding its capacities in response to demand from the market. The combination of the new MetalStar 4 and a six-colour MetalStar 2 line that was installed back in 2012 lends a significant boost to productivity. The decision in favour of the MetalStar 4 was clinched by the forward-looking digital technologies it embodies, alongside the possibilities for individual customisation to the company’s particular needs.
Project manager Thomas Meusel is convinced: “The installation of a production line of these dimensions was certainly an exciting project. And it was definitely the right decision to purchase the MetalStar 4. Koenig & Bauer has done a really good job in terms of both digitalisation and ensuring ease of handling for our operators. The press enables true digital networking. The feedback from our printers was unanimously positive from the very first day of production.
It was a bold decision to invest in a press like this in the middle of a pandemic. The challenges for both sides were enormous. Together with Koenig & Bauer we overcame all obstacles and found creative solutions to meet the planned schedule.”
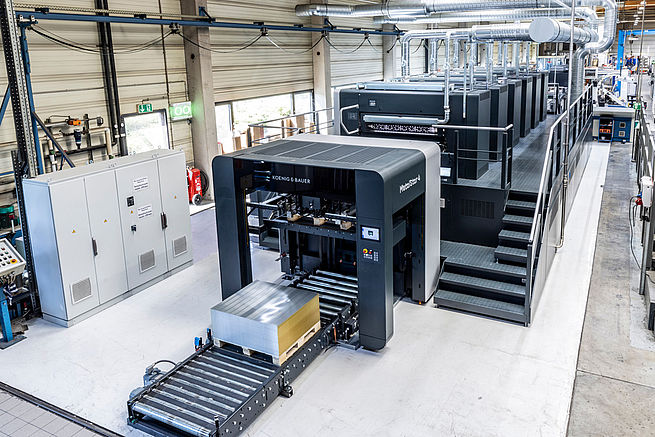
The latest generation of the MetalStar press series boasts a modern design and is a real eye-catcher. The production line at PS PrintService comprises a six-colour MetalStar 4 press, a sheet management system to allow ejection and re-insertion of the metal sheets, and a triple-box stacker with overhead vacuum sheet brake. It combines maximum flexibility with ultimate production quality. The functions of the individual components are automated to achieve the shortest possible job changeover times. As a result, even short runs can be handled profitably.
The line configuration was tailored specifically to the customer’s requirements. Operation of the MetalStar 4 was shifted to the drive side so that the consoles of the new line and the existing MetalStar 2 could be installed on the same side for maximum convenience. The DensiTronic colour measurement and control system, which guarantees perfect adherence to the required colour values and automatically proposes any necessary corrections during production, was configured for use with both lines at PS PrintService. At the same time, the MetalStar 4 is equipped with an efficient ink mist extraction system that removes arising ink mist directly at the source, this being at the inking unit itself.
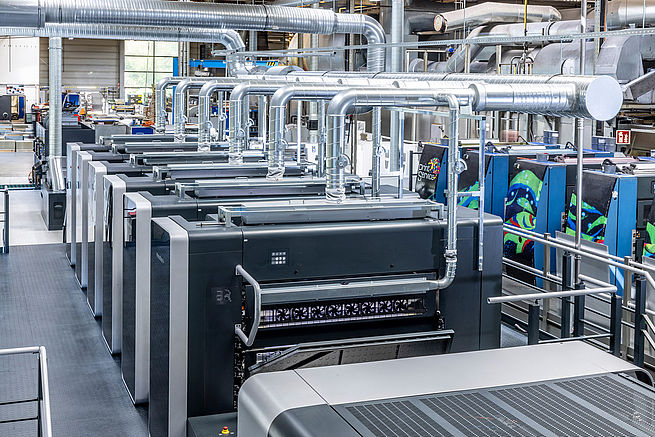
A further step towards full digitalisation
Managing director Christel Rauh explains: “I am delighted! It prints according to the same principles as our ‘old’ press, namely in offset, and I hope that is something that will remain with us for many years to come. Offset is after all a process where you can still ‘feel’ what printing really means. Even so, the latest technologies also represent the next step in terms of Digitalisation 4.0. They have enabled full integration between job management, pre-press, production and controlling.”
“The MetalStar 4 makes work easier for the printers! Plate changes, roller washing, adjustments and reaction times – everything is so much faster. It takes less time to prepare the upcoming jobs with LogoTronic and they are then ready to be called up immediately. I can control and monitor everything absolutely intuitively using the new console. The new system is a huge leap forward compared to the older line,” adds printshop manager Daniel Suffner.
The MetalStar 4 at PS PrintService is equipped with the following features:
ErgoTronic console
An intuitive user interface on all touchscreens, together with ergonomically designed operating panels, simplifies operation. At the ErgoTronic console, the heart of the operating system, all functions can be controlled conveniently by using a 23-inch touchscreen monitor. For example, job changeover programs can be selected and new print jobs can be prepared. The 75-inch wall screen displays the results from the measuring systems.
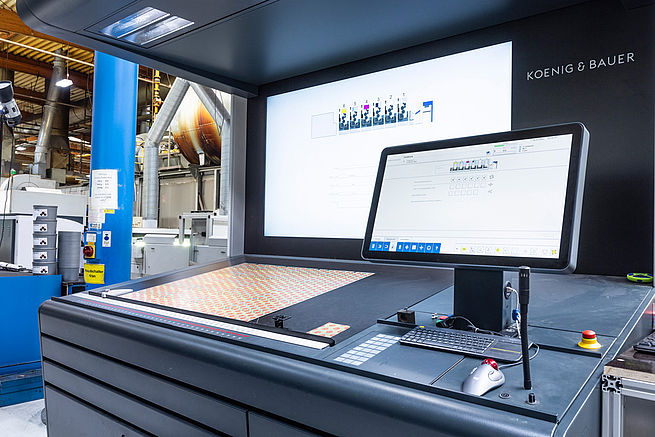
LogoTronic job management
The LogoTronic job and master data management system provides for continuous documentation and the automatic communication of job data from pre-press by using a CIP link to the press. All data for repeat jobs are saved reliably.
SIS – Sensoric Infeed System
The MetalStar 4 is equipped with the DriveTronic SIS sidelay-free infeed system. The metal sheets are allowed more time to settle and align themselves at the infeed. The SIS system excels with all kinds of substrates, whether thick or thin metal sheets, scroll sheets or aluminium.
Makeready optimisation
The MetalStar 4 facilitates even shorter makeready times. The optimised fully automatic plate changing system FAPC is able to change all six plates in just 2.5 minutes. The plates are changed in three cycles, irrespective of the number of printing units involved. The process is controlled conveniently on the ErgoTronic console. The CleanTronic Synchro washing system, in combination with DriveTronic SRW (Simultaneous Roller Washing), permits fully automatic and parallel washing of all inking units, blankets and impression cylinders.
New in metal decorating – pneumatic ink ducts
Pneumatic ink ducts are a brand new feature. They stop the ink keys from ‘sticking’ and thereby add to both the reliability and service life of the setting elements. The intervals between time-consuming cleaning and recalibration of the ink keys have also been extended. In production processes with highly reactive UV and UV LED inks in particular, this represents a significant improvement.
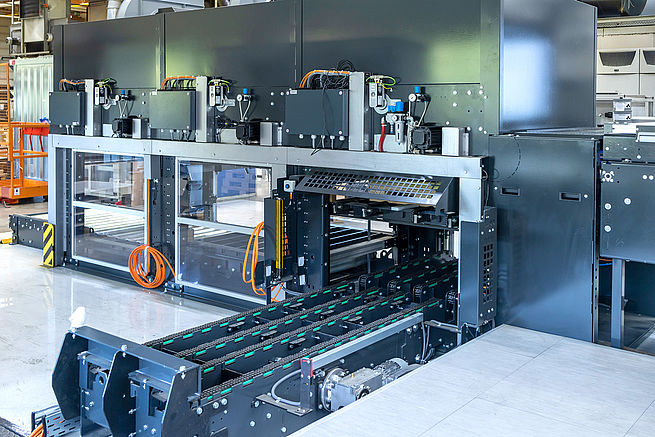
Triple-box stacker
PS PrintService has once again chosen a triple-box stacker with dynamic overhead vacuum sheet brake. Makeready sheets are ejected into the first box. The full pallets are removed to the side by way of a chain conveyor. The second stacker box has been designed to be used for either the ejection of flawed sheets detected by the camera inspection systems or the collection of good sheets, as required. The third box is a good sheet box and can be used in conjunction with the second stacker box to realise the non-stop stacking of good sheets. All three stacker boxes feature automatic format adjustment.