At the beginning of May, KBA-MetalPrint organised a branch symposium in the Austrian town of Kufstein over a period of several days. Alongside informative technical presentations, the agenda included live demonstrations of the newest 6-colour MetalStar 3 UV line in production at local metal packaging specialist Pirlo. The symposium took place parallel to the trade fairs METPACK and Interpack, so as to enable as many prospective users as possible to gain a first-hand impression of the new features of the MetalStar 3 and to combine the event with their visits to the trade fairs.
A very pleasing number of printers took the unique opportunity to attend the symposium. KBA-MetalPrint and Pirlo were overwhelmed by the interest, and were able to welcome more than 100 participants from a total 24 different countries.
One central topic of the event was efficiency maximisation in multicolour printing. In daily practice, it is not merely the printing press, but rather the entire production process which determines efficiency and the quality of results. This all rests on the selection of appropriate consumables and process standardisation. Competent quality control and workflow automation are similarly very important. Accordingly, KBA-MetalPrint invited a number of its closest partners to give presentations during the event, starting with Sun Chemical, the new technology partner of KBA-MetalPrint in the field of metal decorating inks.
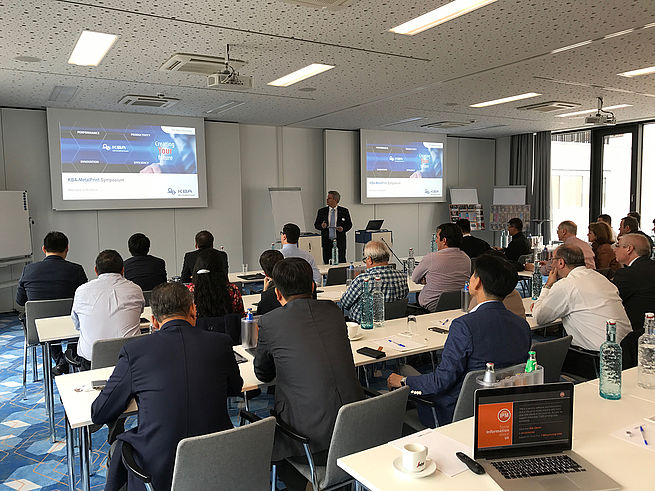
Various technical presentations during the KBA-MetalPrint symposium were concerned with ways to further enhance the efficiency of metal decorating lines.
Sun Chemical took a closer look at the “ink kitchen of the 21st century”, and at how to minimise the time spent on the mixing of spot colours. The objective is to achieve the desired tone at the first attempt and thus to avoid expensive press downtime. Information was also conveyed on the benefits and scope of application of “monopigmented and high-performance inks”. The company offers an extended colour space for the basic Pantone colours, so as to be able to achieve better reproduction on tin substrates. The so-called high-performance inks from Sun Chemical use pigments with very good to outstanding resistance properties. The inks are thus highly resistant to light, heat, organic solvents and sterilisation processes.
Michael Müller from IPM Müller und Resing GmbH captured the attention of his audience with a presentation on the topics of process standardisation and quality management in metal decorating. He introduced the concept “Living PSO”, the core of which is employee qualification to facilitate application of the relevant processes in everyday production. IPM supports companies in the introduction and implementation of standardised and industrial print production along the whole process chain from the PDF files and digital proofs through to CtP and the printing press.
With regard to quality control, Damian Pollok from ISRA Vision AG presented inspection solutions for the field of metal decorating. He began by discussing the benefits of the widely known print inspection system DecoStar, which is already in use on numerous MetalStar press lines. Subsequently, he addressed also the new CoatStar system: A coating image inspection facility characterised by simple handling and a high degree of automation, which can be retrofitted relatively easily to an existing coating machine.
Another innovation was the subject of a technical presentation on LogoTronic Professional – a CIP4-capable production planning and control software for interaction between shop floor and top floor. The software solution developed by KBA permits bidirectional communication with the console of the MetalStar 3. It is thus possible to send not only presetting data (CIP3) from pre-press to the console, but also the complete job data (CIP4) from a management information system (MIS). At the end of production, the relevant data can be saved together with the press settings in the central LogoTronic Professional database. In case of a repeat job, this data can be recalled to shorten makeready time on the press. With the functions SpeedWatch and PressWatch, furthermore, the software serves production management and monitoring. The production data from the press are collected and evaluated automatically. Optionally, they can also be sent to the MIS via a corresponding interface for final cost accounting.
The technical discourse was rounded off by the presentation given by Thomas Groß on the MetalStar 3 innovations which had just been spotlighted at METPACK in Essen. This referred above all to the automation solutions DriveTronic SIS (Sensoric Infeed System) and RBC (Rapid Blanket Change). The presentation went beyond a mere function description and explained how much makeready time can be saved compared to an older MetalStar 2 press, and thus how much extra production time can be gained by users of an ultra-modern MetalStar 3 press in combination with the new features.
To conclude, Pirlo provided an overview of its company group with the three locations Korneuburg, Pionki and Kufstein. Founded in 1908, the family-run business has always combined tradition and innovation, and has built up a national and international reputation as a supplier of modern metal and plastic packaging. It produces individually designed tin cans and laminated tubes for the chemical/engineering, cosmetics, pharmaceuticals and food branches, among others. More than one hundred years of experience and the vast potential of a committed workforce are the basis for constantly new packaging solutions. The company motto is quite appropriately “If anyone can – we can!” This is borne out by countless patents and awards from recent years, including the WorldStar Award 2016, the Green Packaging Star Award and the Austrian State Award for Smart Packaging.
The afternoon was reserved for a final highlight of the event, namely live production demonstrations on the new 6-colour MetalStar 3 UV line now used by metal packaging specialist Pirlo in Kufstein with the features
- FAPC – fully automatic plate changing
- CleanTronic Synchro – automatic simultaneous washing of the blankets and impression cylinders
- DriveTronic SRW – simultaneous roller washing
- ErgoTronic ACR – automatic camera-based register system
- DensiTronic Professional – automatic online colour measuring system
- MetalCure UV - KBA UV dryer system
and the innovations unveiled at METPACK
- DriveTronic SIS (Sensoric Infeed System) – sidelay-free infeed
- RBC (Rapid Blanket Change) – automated blanket changing
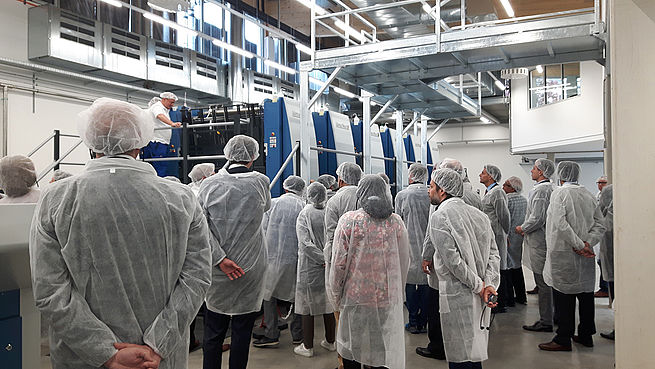
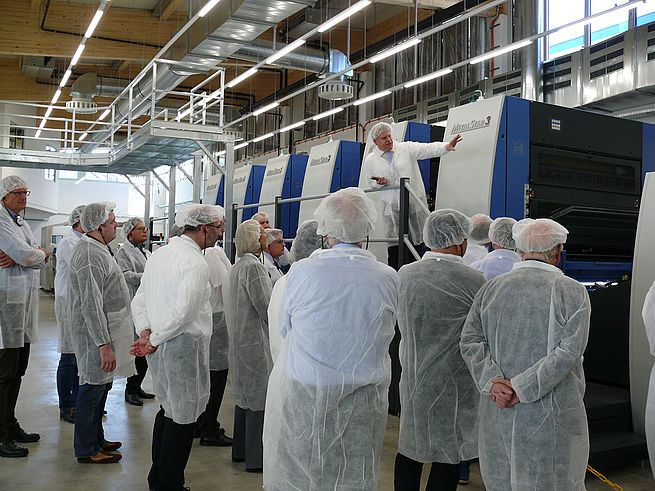
The guests were treated to a demonstration of the press in full production, and were subsequently able to watch a job changeover with ink replacement in two of the six units. The average job changeover time for a four- to six-colour job was approx. 25 minutes, including the time for setting of the registration and colour. The culmination for the symposium participants was a demonstration of automated blanket changing with the new RBC system (Rapid Blanket Change). Tool-free, program-controlled blanket changing now takes only two minutes per printing unit, cutting previous time requirements by more than half! After the practical demonstrations, visitors had the opportunity to take a closer look at details on the press. Specialists from KBA were also on hand to answer any questions about the individual features.
Print instructor Reinhard Walther demonstrated automated blanket changing with the new RBC system (Rapid Blanket Change)
The symposium was very well received by the customers. Special praise was given for the ideal combination of theory and practice, with both technical presentations and informal discussions with the speakers during and after the event. Most impressive, however, were the live demonstrations of cutting-edge high-end technologies for metal decorating and the associated potential for further enhanced efficiency.